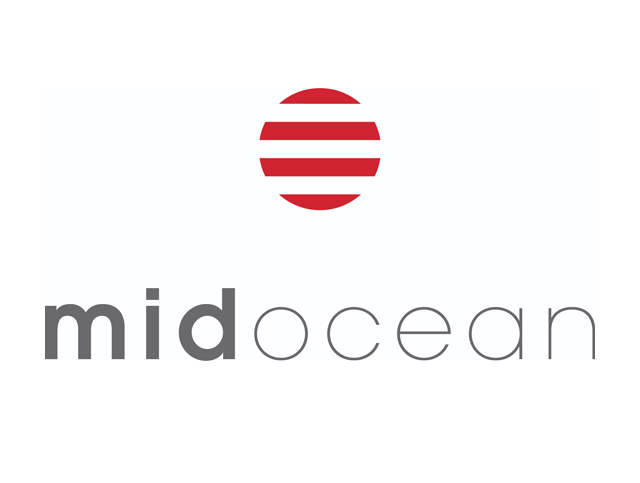
A new production facility offers great opportunities to scrutinize existing processes. Midocean grabbed that opportunity with both hands. Together with Quinso, the wholesaler developed an innovative logistics concept. The result? “Our production capacity has increased and as a result we are now setting the standard in the industry.”
The moment of truth for midocean. Because after years of preparation, planning and construction, the new production facility in Poland was officially inaugurated. The building in Ruda covers 35,000 square meters, with two hundred machines, fifteen printing technologies and one and a half kilometers of assembly line. The control of that assembly line, including integration with warehouse and office floor, is the result of an intensive collaboration between midocean and Quinso.
From manual to automation
“When we moved to a production facility in Chorzow, Poland, ten years ago, we wanted to grow to two hundred employees there,” says Bas Zeegers, supply chain manager at midocean. “But now we count over eight hundred employees.” So a new production facility was inevitable and also provided a great opportunity to innovate. “This was the moment for us to improve the logistics within our print shop,” said Hans Kramer, the organization’s IT director. At that time, they were processing between five hundred and one thousand orders daily at midocean, each of which was moved manually from one station to another. Zeegers: “Items being printed go through roughly six to as many as 15 stations. You can imagine that a lot of time went into that logistical operation, not to mention the buffer zones and possible error proneness.” And so midocean opted for a brand new and automated logistics system, in which a star role is reserved for the assembly line.
Innovate together with Quinso
The new process works as follows: a Web order comes in, which ends up in SAP Advanced Planning and Optimization (APO) through SAP ERP and the design department. Then the order is picked and moves onto the assembly line, where the critical part begins; the item on the assembly line must travel the correct route and end up at the correct workstation. Midocean hooked Quinso to bring about that intelligence.
“After an extensive selection process, Quinso came out on top,” Kramer says. “It was a sum of their experience, the speed in which they were able to implement the solution and the personal click.” Moreover, Quinso was the only party that proposed working with SAP Manufacturing Intelligence and Integration (MII), a relatively unknown system for shopfloor integration. Zeegers: “We asked an independent expert to compare the proposals of three suppliers. He chose Quinso without question. That was the deciding factor.”
Support through Design Thinking
The project started in January 2017. This gave the team seven months to get everything ready before opening; from establishing process flows to implementing SAP MII, including integrations with SAP ERP, SAP APO and the Conveyor Control System. Says Zeegers, “The existing, manual logistics flow had about sixty flows, and that is obviously not do-able in an automated system. That’s why Quinso organized inspiring Design Thinking sessions, during which we poured all those loose flows and exceptions into four happy flows and an exception flow, resulting in a logistics concept that everyone was behind.” That thorough preparation allowed the team to implement the solution on time and on budget. “This part of the logistics project has not been exciting for a moment,” Zeegers looks back.
Ready for the high season
Since the opening of the production facility in Ruda, control of the assembly line has been running smoothly. The orders pass automatically through all workstations, with the right print job with the right printing technique ending up on the order. “Despite still being in transition in terms of change management, we are already running more production than at our previous location,” says Zeegers. “We expect productivity improvements of between twenty to thirty percent soon,” he said. His colleague adds: “We would never have been able to run the upcoming peak season in our old building, but now our logistics apparatus is all set.
Midocean: Quinso is a committed no-nonsense partner
Midocean is currently focusing primarily on the human side of change, as it is challenging to get eight hundred employees to work differently than they were used to for years. “Quinso’s commitment comes out strongly in this,” Kramer says. “After all, the consultants find it just as frustrating as we do when an employee still tries to do something manually.” Zeegers adds: “The project really felt like a team assignment, with Quinso continuously guiding us to stay within the solution and within the scope of five flows. Not with thick reports or endless presentations, but simply by doing, keeping an overview and always remaining critical. With our modern production facility, we now set the standard in the industry. Quinso helped us take that step, and on a much broader level than just automation. We are now ready for the future.”
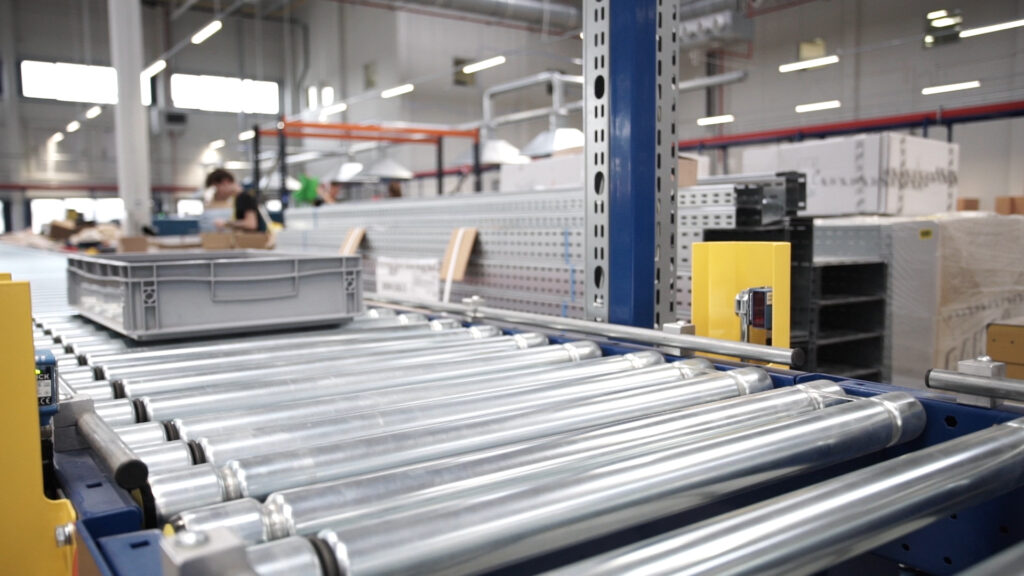
About Midocean
Midocean is a wholesale distributor of promotional items. Headquartered in Ede, the Netherlands, the organization serves the entire European market from local sales offices in Spain, Germany, Hungary, France, Italy and the Netherlands. Since its founding in 1965, midocean has evolved into a one-stop shop including design department and print shop, where items are provided with logos or other advertising messages. The organization ships orders throughout Europe within 24 hours, making it a front rummer in the market.