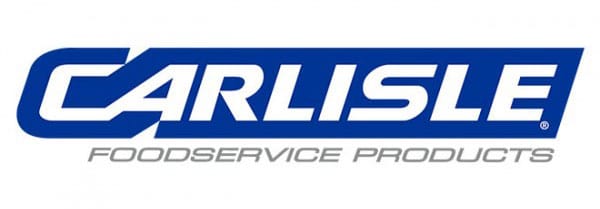
In 2011, Carlisle Hardcast Europe chose SAP ERP, which completely optimized the production company’s top floor. In October 2014, it was the shopfloor’s turn. Production forms and pens gave way to sophisticated screens and the latest software. “Efficiency on the production floor has increased dramatically,” said Rob Reeve, Managing Director of Carlisle Hardcast Europe. “Thanks to Quinso, there is now a robust foundation for Lean Manufacturing.”
CARLISLE® CM Europe combines the strengths of the European subsidiaries of CARLISLE® Companies Incorporated, a publicly traded global company. The CARLISLE® Companies Inc. develops, manufactures and markets a wide range of products serving a variety of niche markets: commercial roofing, energy, agriculture, mining, construction, aerospace and defense electronics, food, healthcare and plumbing maintenance.
The secret to the success of CARLISLE® Companies Inc. is: decentralized companies run by entrepreneurial thinking and action and management teams that know how to bring innovative product solutions to the various needs of our customers. The global team of more than 12,000 employees work daily with the best products of superior quality and one with exceptional service to continuously improve the value of the CARLISLE® brand.
1. A powerful and robust Shopfloor Control System.
Carlisle Hardcast Europe distinguishes three stages in the production process: (1) producing the adhesive, (2) cutting the tape and (3) packaging the finished product. Control of this process was previously entirely paper-based. Now screens have been installed on the production floor. The operator starts an order and the system indicates exactly which products
2. Practical and lightning fast Labeling Software.
A direct link was made between NiceLabel software and SAP ERP 6. Labels are therefore generated immediately and automatically when an order is started. Reeve: “That works great. There are always just enough labels ready, for just the right product. And if a label gets dirty or tears, you just print a new one. Previously, this process was controlled manually. That was labor-intensive and error-prone, because we have an enormous variety of labels. Now it’s done at the push of a button.”
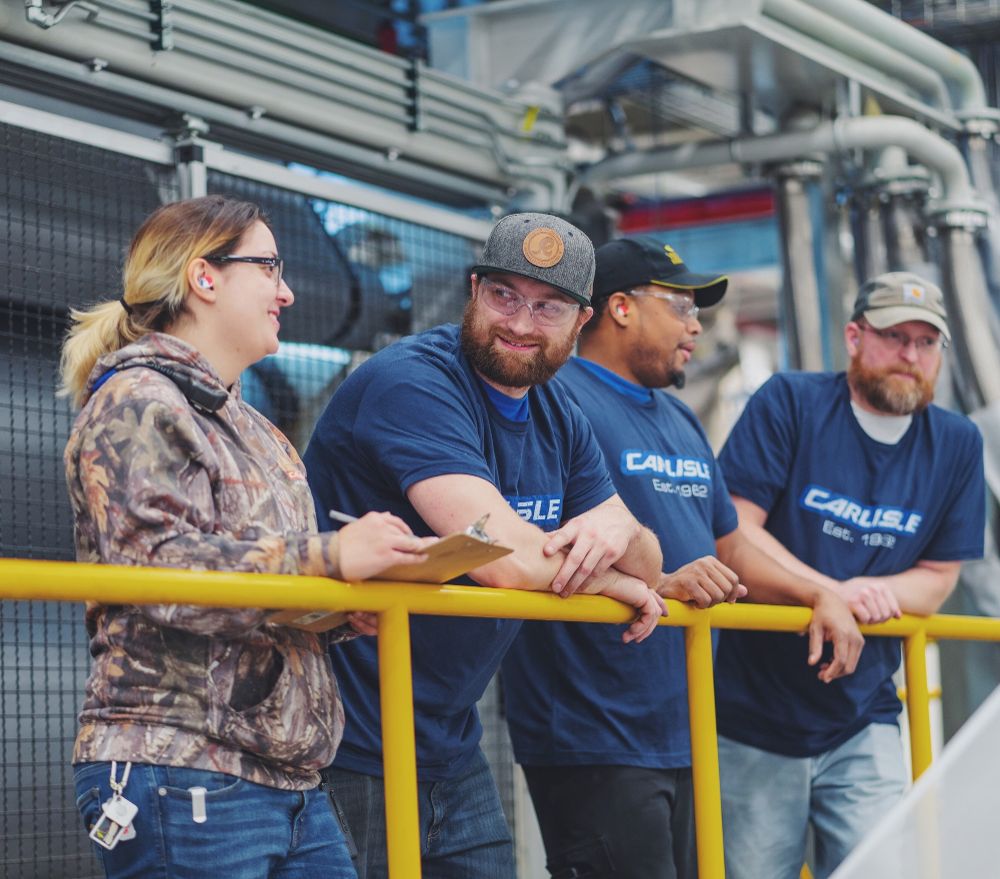
Processes without noise
With its ERP system and Shopfloor Control System, Carlisle Hardcast Europe has laid a robust foundation for Lean Manufacturing. Reeve: “Our production process now runs one-to-one with the automation; the noise of manually processing information is completely gone. We don’t have to do
prepare production forms or labels anymore, and we no longer have to report back orders. Customer service finds the status of an order in real time in the system; that saves another walk downstairs. With this new way of working, we save about sixty hours of administrative work each week. And perhaps more importantly, because there are no more waiting times, production lead times have been reduced from 10 to five days.”
The power of real-time
Wouter Vervoort, Project Manager at Quinso, emphasizes the enormous benefits of real-time analytics. “The Shopfloor Control System records everything. As a result, the reliability of tracking and tracing finished products has increased to 100 percent and machine hours no longer need to be recorded retrospectively
. The information in the system contains valuable insights that help to make even more efficient use of the production floor. When was production unplanned? And what was the cause of that? Soon Carlisle Hardcast Europe will see that at a glance through the Overall Equipment Effectiveness (OEE) report.”
Quinso: proactive and pragmatic
Although Carlisle Hardcast Europe ‘s implementation process is not yet complete, the company is already looking back on a successful project. Reeve: “Quinso has an unprecedented specialized knowledge of manufacturing. They are engaged, master the intricacies of project management, take on a directing role and
make things negotiable. Because of that pragmatic and proactive approach, the consultants were not outsiders for us, but a perfect addition to the team.” Vervoort can certainly agree: “It’s really about the team; that’s how you lay the best foundation for success.”