Customers are demanding more and more in terms of speed and sustainability. Continuously optimizing the process and making it more sustainable is crucial to meeting that expectation. ORBIS Logistics digitizes and structures the warehouse process, making it more sustainable and efficient.
An inefficient warehouse process creates a lot of waste, such as in time, paper and packaging materials. Digitize all goods movements, from goods receipt to internal movements, outbound flow and even the packaging process. ORBIS Logistics makes it easier to structure and then optimize processes in the warehouse. Employees can also perform their tasks through a user-friendly and flexibly configurable application that can be accessed by different devices.
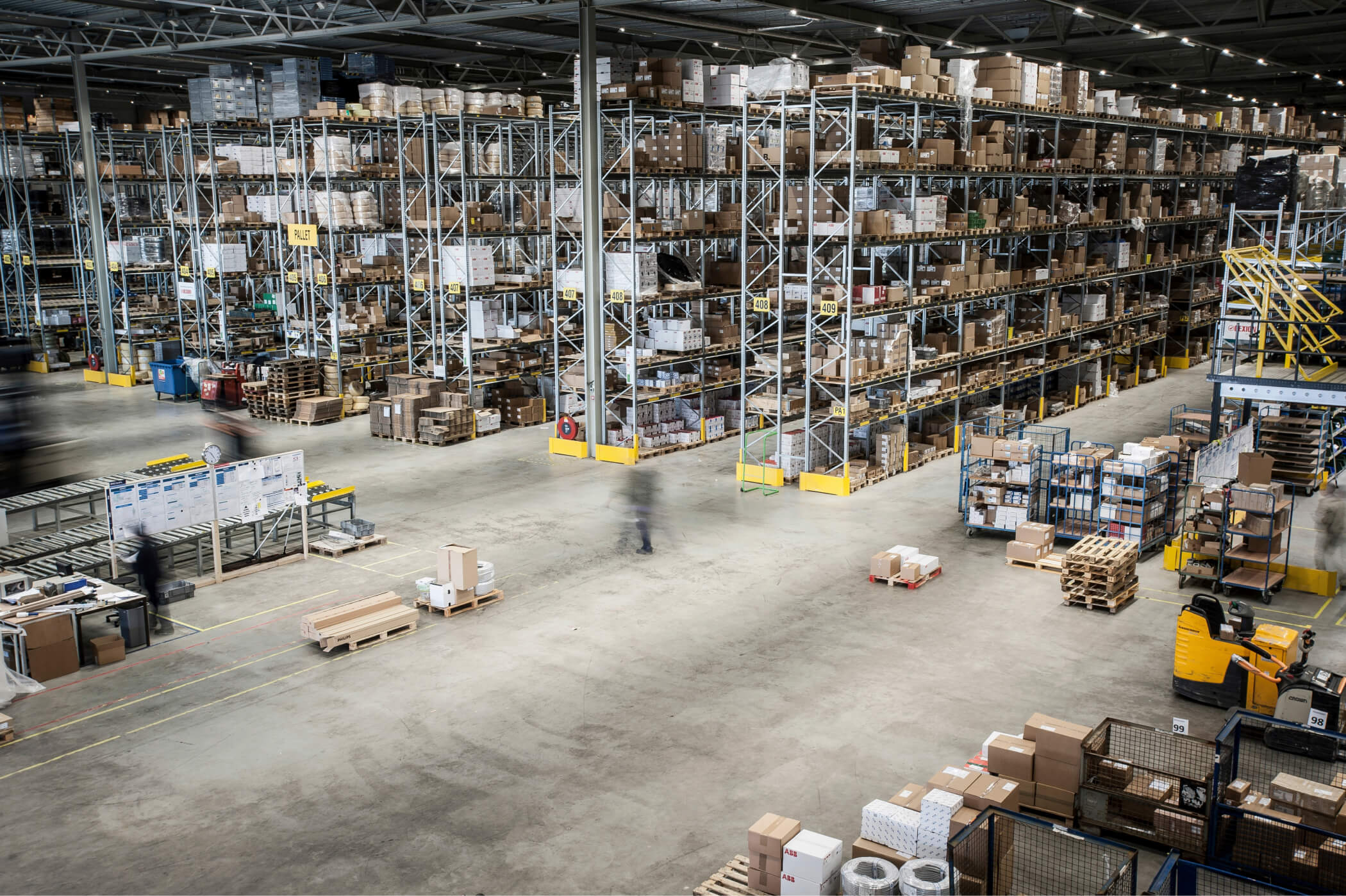
Benefits ORBIS Logistics
- Performing efficient movement of goods within the warehouse
- Integrates with parcel carriers, eliminating the need for manual notification of shipments
- Having real-time visibility into inventory from various vantage points, such as warehouse location and material
- Works accurately and is user-friendly, reducing errors
- Provides visibility into goods movement and speed of deliveries at any time of day
- Promotes sustainability by eliminating the need for paper pick lists
- Packaging module for efficient control and execution of the packaging process
- Integrates fully with SAP ERP, S/4HANA and NiceLabel.
ORBIS Logistics provides insightful and transparent operations as well as a paperless warehouse. With simple implementation, few interfaces and dynamic processes. Want to join us to see how ORBIS Logistics can streamline your processes and achieve a unified way of working? Contact us! We are always happy to assist you.
ORBIS Logistics en NiceLabel
NiceLabel is a certified solution for SAP and comes with a standard integration with ORBIS Logistics. Users can quickly and easily create labels via drag and drop. The result? Real-time labeling: the moment a pallet arrives, the correct label rolls out of the printer immediately.
